The Fujifilm Group is actively recycling resources by establishing recycling schemes for used products such as QuickSnap™ cameras and multifunction devices, as well as recovering silver and other materials from our products to reuse them. We have been promoting our comprehensive efforts in recycling and waste reduction taking account of product life cycles, such as by ensuring product designs incorporate consideration of the 3Rs (reduce, reuse, recycle), loss reduction in the production stage, collection-reuse-recycle of used products, and converting wastes into valuables or recycling them.
Following the flow of the transition to a global recycling economy, the Fujifilm Group established its Resource Recycling Policy in fiscal 2024. Based on this policy, titled “Aim at not using resources from new mines*1,” we are minimizing the usage of resources from new mines and promoting resource recycling by expanding policy coverage to the entire product life cycle (from materials procurement, manufacturing, and usage,through to disposal) in addition to the current target “waste reduction in manufacturing.
- *1 Mines for non-renewable oil and mineral resources
At FUJIFILM Corporation Fujinomiya site, where we conduct research, development, and manufacturing of medical X-ray films and various functional films, a waste reduction project was launched across the entire site in 2020. Over the three years, the amount of waste was reduced by approximately one-third. The project focused on reducing PET (polyethylene terephthalate) related waste, which constitutes a significant portion of the waste generated at the site, by targeting “waste reduction in the PET resin manufacturing process” and “promotion of PET-related waste recycling.”
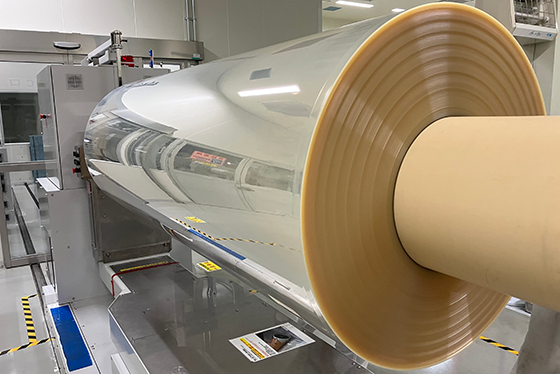
Rolled PET film used as a raw material for various functional films
In our Office Solutions business, which provides such products as multifunctionl devices and printers, based on the concept of “used products are valuable resources, not waste,” we established the Closed Loop Recycling System in 1995. The system demonstrates our determination to pursue resource recycling that takes account of the entire product life cycle—from product planning, development, manufacturing, through to disposal.
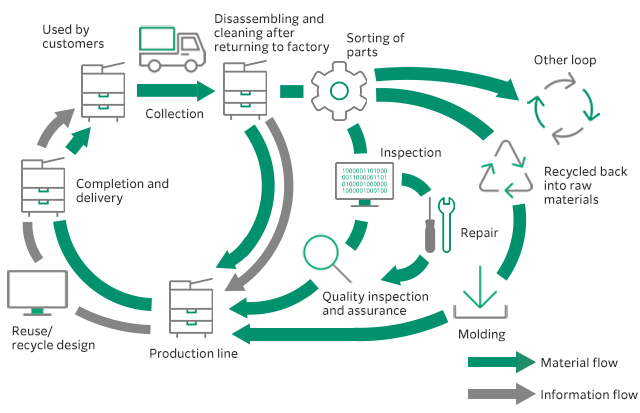
In the Consumer Healthcare business, which provides functional cosmetics and supplements such as the “ASTALIFT” series, we are working to reduce CO2 emissions and waste by reducing the amount of plastic used through measures such as offering refills for containers of the “ASTALIFT” series.
Developed with the concept of “easy to take pictures anytime, anywhere, by anyone, the one-time use camera QuickSnap™ is designed with environmental consideration through “thorough reduction of the number of components,” “design of components that can be used in multiple models,” and “product design that does not use screws or adhesives based on the premise of recycling.”
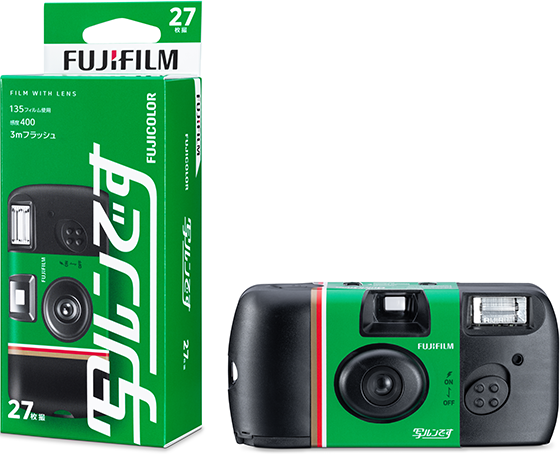