To promote sustainable procurement activities, the Fujifilm Group has designated a Sustainable Procurement Promotion Program that is run cyclically in the following four steps.

To help our suppliers gain an understanding of the Fujifilm Group’s CSR approach and requirements, instead of just disclosing our Code of Conduct and Procurement Policy on our website, we hold supplier briefings to explain our policies and standards directly, and request for their compliance. To go even further, we also send out our Code of Conduct to the suppliers and receive their consent forms on a regular basis to disseminate our approach. (Disseminated basically once in three years and at the revision of Fujifilm Group Code of Conduct)
To identify sustainability-related risks and issues concerning suppliers, the Fujifilm Group conducts regular risk assessments and requests suppliers to carry out self-checks. Such assessments are carried out on critical suppliers determined by procurement amounts and replaceability of the procured items, as well as on suppliers in the priority risk management regions,*1 such as China and Asia. Some of our Group companies’ tier 1 suppliers are trading companies. In this case, we also ask the production companies (production sites) that supply to the trading companies to carry out self-checks. In addition to evaluating existing suppliers, we also conduct assessments on sustainability-related risks when selecting potential new suppliers.
Also, we started using a risk screening tool provided by an external vendor in fiscal 2022 for more efficient identification of sustainability risks concerning suppliers to enable a prompt response in the event of a risk-related incident. With this tool, we are now screening legal violations from the viewpoints of social and governance in our supply chain.
In addition to the self-checks described in section (2), an onsite risk assessment takes place individually for high-risk suppliers—determined by the self-check results and day-to-day procurement practices. Following the assessment, we submit improvement requests as needed and provide support for such improvements. In China and Asia, our internal expert teams conduct onsite visit and check for sustainability activities by the supplier and provides advice on making improvements. We position this onsite review by expert teams as equivalent to a Responsible Business Alliance (RBA) audit. Based on the check results, we encourage the suppliers to proceed with improvements, and thereby promote the Fujifilm Group’s sustainable procurement methods across the whole supply chain.
- *1 The Fujifilm Group identifies risk areas within its supply chain from the viewpoint of sustainability by analyzing the regional environment, social risks and the relevant regulations in countries and regions.
To ensure viable sustainable procurement, Fujifilm classifies suppliers into different levels, as shown in the diagram on the right, to apply appropriate measures.
Level 1 covers all suppliers and we request them to comply with the Fujifilm Group's Approach to CSR.
Level 2 covers critical suppliers, as determined by procurement costs along with the substitutability of the items they provide. These suppliers are requested to carry out regular self-check risk assessments.
Level 3 covers high-risk suppliers, determined by the self-check results and day-to-day procurement practices, and the “most critical suppliers” who are significantly important to our business from the viewpoint of procurement costs and the rarity of the procured items. We visit these suppliers in the order of criticality to assess risks, request improvements, and provide support. Also, use of an external risk screening tool enables us to detect sustainability-related risks among our suppliers, in order to make an early response in the event of an incident.
The Fujifilm Group disseminated its Requests to Suppliers (Fujifilm Group Charter of Corporate Behavior and Code of Conduct) to its suppliers in Japan, China and other Asian countries, which are the focus of its risk management efforts, and collected consent forms from 867 suppliers.
We requested critical suppliers to carry out self-checks. In fiscal 2023, we enhanced the explanations for the questions in the self-check list, particularly for questions where suppliers scored low in the previous year. This was done to encourage a correct understanding of the questions as well as the intention of our sustainability initiatives. We received self-check responses from 995 suppliers (1,493 sites), marking a 96% response rate. The fiscal 2023 self-check results did not reveal any significant risks related to child labor, forced labor, or freedom of association.
At the same time, we also conducted the information security survey (self-check), which we started in fiscal 2022. This is to understand the security risk management status in our suppliers, in response to reports that cyberattacks on supply chains were affecting production activities and supplies. The number of responding suppliers was 1,064 in fiscal 2023.
We have been continuing supplier risk assessments using the risk screening tool we first implemented in fiscal 2022. The tool is used for suppliers in the priority risk management regions, including Japan, China, and the rest of Asia, and the number of suppliers subject to the tool has increased from 600 in fiscal 2022 to approximately 3,000. As a result, we identified 25 cases of risks among our suppliers. For each case, we discussed with our procurement divisions to determine whether the risk would impact us and whether to take countermeasures. We then requested the supplier to make improvements and undertook any other necessary actions.
For all suppliers that conducted self-checks and responded to the information security survey, we sent a feedback sheet that included a score compared to the overall average (conformance rate) or evaluation level. For suppliers with a conformance rate below 80% or where non-conformance was identified for high priority items, we provided advice on how to improve any identified issues in the feedback sheet and encouraged them to make improvements. Further, for some suppliers, we conducted follow-up interviews to directly confirm the actual situation regarding the non-compliant items. We ask the suppliers to resolve the issues as necessary, and then confirm the improvement status.
In fiscal 2023, we conducted such follow-up interviews with 44 suppliers through face-to-face meetings, telephone calls, and e-mails based on the fiscal 2022 self-check results. We identified several cases where the sustainability-related practices referred to by the self-check list are in place but not explicitly stipulated in written policies or company rules. We explained to these suppliers that proper documentation is necessary for thorough implementation. In the fiscal 2023 follow-ups, we identified that 31 of the 44 suppliers we interviewed in the previous year had improved their conformance rate. We also improved the 2023 self-check questions based on insights gained from interviews with the suppliers, such as their level of understanding of the questions and the issues they pointed out.
Reviewing the self-check results from the previous year and considering the procurement amount and business status of our suppliers, we identified 65 suppliers in China and Vietnam as requiring risk assessment. Expert teams from our production sites provided onsite visits and checks to 50 suppliers out of 65.
In onsite visits and checks during fiscal 2023, as usual we visited suppliers' production sites and their employee dormitories. We also inspected their labor agreements and related documents.
These assessments identified the following issues and continuously confirmed that they had been improved.
Categories | Issues |
---|---|
Occupational safety and health | An emergency evacuation route next to the finished goods storage area was blocked by items. |
Human rights | Employees’ consecutive days of work (12 consecutive days) |
Environment | Insufficient separation of wastes |
Corporate ethics | Inadequate internal complaint or whistle-blowing system |
We confirmed that such critical issues were improved by the end of that fiscal year for all suppliers where onsite assessments had been conducted. We continue monitoring the suppliers’ progress for those issues that require some time for improvement.
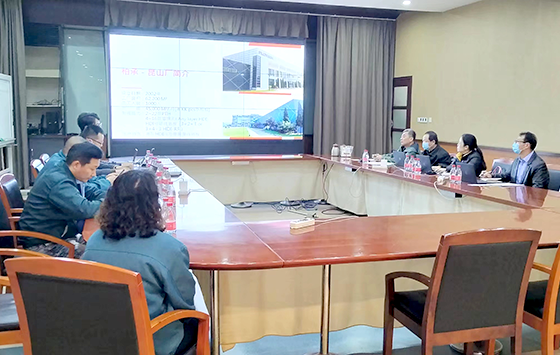
Interviews with suppliers
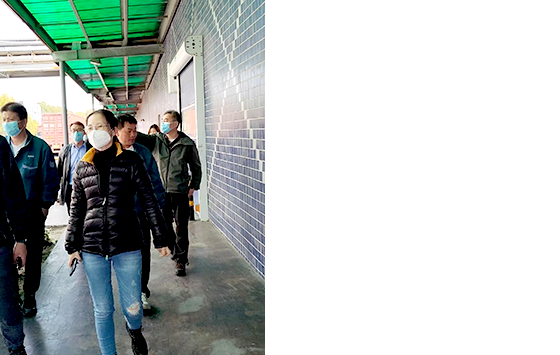
Visit to supplier's production site
In supplier briefings in Japan, we raised awareness of the importance of appropriate chemical management in the supply chain. We also provided concrete information on the latest trends concerning procurement-related laws and regulations, and promoted thorough communications on the regulated chemicals contained (or not contained) in the procured goods. We always opened the briefings with an explanation of the importance of sustainability and our efforts in sustainable procurement. We also fostered understanding of the Fujifilm Group Charter of Corporate Behavior and Code of Conduct and requested suppliers to submit their consent form for the Code of Conduct. Following on from the previous year, the fiscal 2023 briefings were held as a webinar. A total of 139 participants from 106 companies attended the webinars.
In fiscal 2023, using a hybrid format of face-to-face and online meetings, we provided a briefing on sustainable procurement to suppliers of our major production site in China. The briefing was attended by 212 people from 168 companies, including both tier 1 suppliers of materials and subcontractors. The supplier briefings explained the Fujifilm Group’s procurement policy, the sustainable procurement procedure in China, examples of how to meet the requirements, and descriptions of self-check questions. According to the participant questionnaires, 95% of the suppliers responded that they had learned a lot from the briefing.
Laws and regulations in China have been tightened in recent years, and the country is particularly important for our Group, having the second highest procurement amounts as well as the highest number of suppliers after Japan. For these reasons, we continue to promote sustainable procurement activities in China.
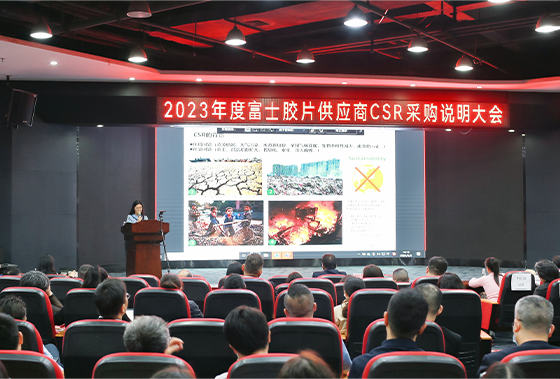
The briefing on sustainable procurement to suppliers held in China
Activity | Item | FY2021 | FY2022 | FY2023 | FY2024 target |
|
---|---|---|---|---|---|---|
Target | Result | |||||
Dissemination of Code of Conduct, Collection of consent forms | Number of suppliers’ consent forms collected | 204 | 733 | 300 | 867 | 400 |
Self-check regarding sustainability | Number of suppliers responded / Number of sites responded (Response rate) | 368 suppliers / 558 sites (90%) | 774 suppliers / 1,262 sites (92%) | 1,000 suppliers | 995 suppliers / 1,493 sites (96%) | 1,000 suppliers |
Percentage of suppliers with 90% or over conformance rate | 77% | 70% | 90% or over | 69% | 90% or over | |
Information security survey*2 | Number of suppliers responded | - | 722 | 1,200 | 1,064 | 1,000 |
Onsite visit and check | Number of suppliers evaluated (Plan achievement rate) | 33 (62%) | 24 (57%) | Plan achievement rate 100% | 50 (77%) | Plan achievement rate 100% |
*2 Information security survey was started from fiscal 2022.
Conformance rate | Evaluation | Percentage of conformant suppliers |
---|---|---|
90% or over | Almost satisfy the requirements of our Code of Conduct | 69% |
80% to 89% | Some issues need improvements | 22% |
Less than 80% | Need our supports for improvement | 9% |
Japan’s logistics industry faces serious social issues, such as long working hours by courier drivers, death from overworking, and environmental and safety issues caused by poorly maintained vehicles. These problems are caused by the increasing trend of internet shopping and the home delivery demand.
FUJIFILM Logistics Co., Ltd., which is in charge of logistics operations for the Fujifilm Group, has been requesting its logistics partners (tier 1 suppliers) to cooperate in our sustainable procurement for logistics in Japan since fiscal 2009. Through such requests, logistics partners conduct sustainability self-checks and if their conformance rate is less than 90%, FUJIFILM Logistics visits the partner company to offer advice for correction.
In fiscal 2023, we requested 112 suppliers to conduct self-checks and collected the results from all suppliers. Following the revision of the Ordinance on Industrial Safety and Health in fiscal 2023, we added questions to assess logistics partners’ understanding of, and adherence to, the revised contents. For companies that had less than a 90% conformance rate in the previous year, we made an onsite interview and confirmed that the nonconforming aspects had been improved . As a result, all these companies improved their self-check conformance rates.
FY2021 | FY2022 | FY2023 | FY2024 target | |
---|---|---|---|---|
Percentage of companies with 90% or more sustainability selfcheck conformance rate | 95% | 97% | 99% | 100% |
In fiscal 2022, FUJIFILM Logistics focused on improving logistics efficiency through cross-industry collaboration. In fiscal 2023, it continued to implement “long-distance relay trucking,” where multiple drivers change over after covering a set intermediate distance. Relay trucking reduced both the number of vehicles and working hours, as well as minimizing the long-hour working resulting from long-distance single driver transportation.
Since fiscal 2020, FUJIFILM Logistics has been using the GoStop Management System, a logistics service provided by the Japan Weather Association, to support transportation safety in bad weather. We provide our partners with information gained from the system, such as bad weather forecasts and other data that helps determine whether it is necessary to cancel transportation. In fiscal 2023, there were no accidents caused by natural disasters.
Over the years, due to the nature of our founding business, the Fujifilm Group has been working to reduce the environmental impact from our business throughout the product life cycle, from material procurement, manufacturing, transportation, and use, to final disposal. Particularly in material procurement, we are expanding the scope of efforts to include our suppliers through the structure of sustainable procurement.
In the Business Innovation segment, we conducted CSR self-checks at seven production sites across the world, and confirmed that all sites observed more than 90% conformance rate.
In fiscal 2023, the results of the RBA self-assessment questionnaire (conducted at six sites) also stayed at “Low” risk assessment for all sites.
Fujifilm Group's main production sites have been undergoing audits under the Validated Assessment Program (VAP)
of the Responsible Business Alliance (RBA)*3, which is dedicated to CSR in global supply chains.
- *3 RBA (Responsible Business Alliance / Virginia USA) See RBA’s website for details.
Site | Country / region | Status | Expiration date |
---|---|---|---|
FUJIFILM Manufacturing Shenzhen Corp. | China | Silver | April 17, 2027 |
FUJIFILM Manufacturing Hai Phong Co., Ltd. | Vietnam | Silver | February 27, 2027 |
As of December 2024, FUJIFILM Corporation has received the Bronze Medal and FUJIFILM Business Innovation Corporation has received the Gold Medal from EcoVadis*4, a business sustainability ratings provider.
- *4 EcoVadis: The EcoVadis Sustainability Rating evaluates companies' policies and initiatives in four categories: Environment, Labour & Human Rights, Ethics, and Sustainable Procurement.